Resources for Architects, Landscape Architects and Engineers
Through experience gained in supplying millions of square feet of green roofing, a decade of research and an obsessive drive for continual improvement, we have developed evolving best practices for designing green roofs. We are pleased to share these experience with architects and engineers, so that there is no need to reinvent the wheel when it comes to green roof design.
We strongly recommend that you download and reference our Designer’s Checklist each time you design a green roof. This one page list includes design-related issues which may not be obvious but can have a large impact on the success of your project.
FIRE SAFETY
Fire / Spread of Flame – Lab Testing
In January 2008, LiveRoof was tested at UL Labs using a test protocol typically applied to other roof coverings. In this case, a Sedum-populated LiveRoof Standard modular system was installed on top of a plywood deck and subjected to a direct, surface-applied flame for 10 minutes.
After 10 minutes, there was no ignition of the plywood deck and no spread of the flame via the plant material. While the plants in the path of the flame were scorched and reduced to ash, they did not ignite and spread the flame. The LiveRoof soil and the module itself remained intact.
LiveRoof systems populated with succulents are expected to enhance the resistance of a roofing assembly against surface-applied flames.
Fire resistance characteristics pictured in this video are expected for LiveRoof modules populated with Sedums or other succulent plants. Dry grasses or herbaceous perennials may burn and propagate the flame across the soil surface. However, the flame is not expected to penetrate the inorganic soil surface, the plastic module or the roofing membrane assembly below it.
Fire resistance characteristics pictured in this video are expected for LiveRoof modules populated with Sedums or other succulent plants. Dry grasses or herbaceous perennials may burn and propagate the flame across the soil surface. However, the flame is not expected to penetrate the inorganic soil surface, the plastic module or the roofing membrane assembly below it.
Fire Safety Design Standards for Vegetative Roofing
In 2010, the American National Standards Institute (ANSI) accepted GRHC/SPRI VF-1, Fire Design Standard for Vegetative Roofs as an American National Standard. This document provides design and installation recommendations to help eliminate the risk of fire on green roofs. A code change proposal has been submitted to the International Building Code to include this standard in the 2012 edition of the International Building Code. Depending on the plant selections, LiveRoof systems meet the requirements to qualify as generic fire-resistant “Succulent based systems” (4.1.1) or “Grass based systems” (4.1.2).
FM Approved
In July 2011, the LiveRoof Hybrid Green Roof System became the first to be FM Approved according the FM Standard 4477. Developed by FM Approvals, LLC, FM Standard 4477 is the approval standard for vegetative roof systems. It evaluates green roof performance related to fire, foot traffic resistance and water leakage. In addition to testing the LiveRoof system, FM Approvals examined LiveRoof’s manufacturing facilities and audited its quality control procedures to verify that the company produces a consistently uniform and reliable product.
Recognized and respected worldwide, the FM Approvals certification process assures that products and services have been objectively tested and proven to conform to the highest property loss prevention engineering standards. Building owners and facility managers who rely on FM Approved products now have LiveRoof as a certified green roof solution.
The approval is granted to the LiveRoof Standard and Deep Systems populated with succulent groundcovers. For specific information on Approval requirements and compatible membrane assemblies, view our FM Approval Report.
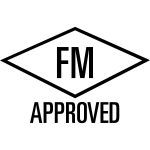
Do you have additional questions about fire safety on green roofs? Your local LiveRoof representative can help.
IRRIGATION DESIGN
Effects of Supplemental Irrigation
While irrigation may only be needed during protracted hot dry weather (to sustain the plants), there are other reasons to install an efficient means of irrigating one’s green roof. Irrigation allows the green roof to be fully optimized. With the ability to irrigate during hot dry weather the rooftop can be turned into one big cooling unit and save money on air conditioning. Remember water liberates 8000 BTU of energy during evaporation (latent heat of evaporation), and pumping water is efficient and cheap, but running air conditioners is inefficient and expensive. The cooling effect derived by irrigating allows for the conservation of energy in comparison to the energy wasted on cooling by less efficient methods.
According to some authorities, and dependent upon the particular climate, during the cooling season the temperature in the room below an irrigated green roof may be reduced 16 to 27ºF compared to a reduction of about 11-13ºF for a non irrigated green roof. This difference is substantial and can mean considerable savings on air conditioning costs. Estimates of cost savings for air conditioning range from 25% to 50% for the floor under the green roof. Irrigating during hot dry weather allows for the optimization of the green roof’s cooling ability.
In rough figures, when an extensive irrigated green roof shows an average summertime temperature of 80 degrees, the same roof without irrigation will average about 100 degrees. Similarly, the membrane below the irrigated roof might fluctuate an average of only 7 or 8ºF during a 24 hour period, while the same green roof without irrigation may fluctuate ± 20 degrees. Less fluctuation may mean less wear and tear via micro-tearing on membranes, and therefore potential extension of the lifetime of the waterproofing membranes.
Judicious irrigation also keeps the green roof plants fat, full and beautiful. This means better coverage, fewer weeds, less labor, and happier owners, occupants, and visitors. It also means lower maintenance costs and safeguards one’s investment in the green roof.
Finally, judicious irrigation should not significantly impact stormwater management as irrigation typically occurs only during low rain/low runoff periods when the roof will dry out quickly from evapotranspiration.
Benefits of Irrigation vs. No Irrigation
- Net energy savings
- Reduced temperature fluctuation (less wear on membrane)
- Less maintenance cost
- Plants will be optimally beautiful
- Avoid plant loss due to drought
- Greater owner satisfaction
Save Water, Irrigate
In his paper, “How Green Roofs Partition Water, Energy and Costs in Urban Energy-Air Conditioning Budgets,” Paul S. Mankiewicz PhD of the Gaia Institute illustrated the hidden relationship of water and energy when he asked the question, “Is it more cost-effective to utilize potable water for cooling than electrical air conditioning?”
He found that the cost of electricity for a ton of air conditioning in New York costs $13.50, while the evaporation of 33 gallons of water produces an equivalent ton of air conditioning for only 26 cents.
Central to his comparison is the fact that virtually all electricity has substantial water cost for its production. Each ton of air conditioning requires 84 kilowatt-hours to produce. In four major cities, this quantity of electricity takes between 24 and 89 gallons of water to generate. On the average, each gallon of water used to cool a structure will save 1.7 gallons of water used to produce the equivalent cooling using air-conditioning.
Overhead vs. Drip vs. Sub-Irrigation
Overhead, matched-precipitation rotor systems are the best for irrigating green roofs, and they do a better job with less water than drip or sub irrigation methods.
In 2011, an irrigation study was conducted in the MSU Plant Science Greenhouses by Bradley Rowe PhD, in LiveRoof green roof modules. Substrates that were watered with overhead irrigation retained more of the water dispersed with less waste than sub-irrigation and drip systems. This is because green roof substrates are designed with coarse-textures for drainage, and therefore do not wick water or move it horizontally very well.
To simplify the placement and speed up installation of irrigation lines, we have developed PipeRunner.
Do you have more questions about best practices for green roof irrigation? Your local LiveRoof representative can help.
JOB SITE SAFETY
Effects of Supplemental Irrigation
Remember, wind uplift should be managed during the entire installation process. High winds can come at any time and will not wait for the installation process to be completed. Be sure to cover materials with appropriate temporary ballast.
Tie-Off Anchors
Green roofs that are not surrounded by a railing or wall of sufficient height to meet local safety codes should include permanent tie-off points for maintenance personnel to safely care for the green roof. Furthermore, access to the roof must be easy and safe. For example, if a fire hatch provides access to the roof, ensure it can be opened easily and exited or entered safely.
Landing Areas and Maintenance Paths
Green roof maintenance should be conducted at least twice monthly during the seasons in which plants are actively growing (typically 8+ months per year). Similarly, rooftop HVAC equipment typically requires regular inspections, and windows along the edges of green roof areas require frequent washing. Designers should take into consideration where regular foot traffic is required and provide pathways or landing areas for maintenance personnel.
RoofStone pavers are recommended as a simple solution for regular foot traffic in the following areas:
At the landing area where personnel will stand on the green roof.
Along walls with windows that will require washing.
Between the rooftop access points and equipment that requires servicing.
Need help planning for safe access for green roof installation and maintenance? Your local LiveRoof representative can help.
PLANTS
Water Sourcing vs. Water Conserving Plants
The LiveRoof Standard and LiveRoof Lite systems are “Extensive” green roof systems. In other words, their soil depth is less than 6 inches. And, while extensive green roof systems optimize evaporative cooling and storm water management (in part because they can dry down between rain events), their shallow substrate depth means that the plants they can support must be extraordinary at resisting drought. Practically speaking, the plants that work best in “extensive” green roofs must be exceptional “water conservers” as opposed to “water sourcers”.
Water conservers are plants that store copious amounts of water in their fleshy stems and leaves. Cacti are the poster children for “water conservers”. They absorb water when available, and conserve it by closing their leaf pores during the day. Their leaves and stems also have a waxy cuticle and relatively little surface area. Water sourcers, on the other hand, are plants that have extensive and deep root systems that go deep into the earth to find water. Good examples of “water sourcers” are prairie plants such as little bluestem, purple coneflower, and prairie dock.
Recommended Plants — Accent & Base Plants
The LiveRoof system is typically vegetated with a palette of deciduous, semievergreen and evergreen “base mix” and “accent plants” that are exceptional “water conservers.” These are succulent, water-holding plants like Sedums, Alliums, Sempervivums, Euphorbias, Delospermas, and perhaps a few other species.
Plants release water as they open their leaf pores (stomates) to exchange carbon dioxide and oxygen gases during metabolism. Most plants perform this exchange as they receive sunlight during the day. The best green roof plants both store water and have a special type of metabolism called Crassulacean Acid Metabolism (CAM).
CAM plants are unique in that under drought conditions their leaf pores are open at night rather than during the day. CAM plants exchange gasses in the dark when it is cooler and less windy. Less water is lost in the calm nighttime air, so CAM plants are up to ten times more efficient with water conservation than non-CAM plants.
Can Native Plants be Used in RoofTop Gardens?
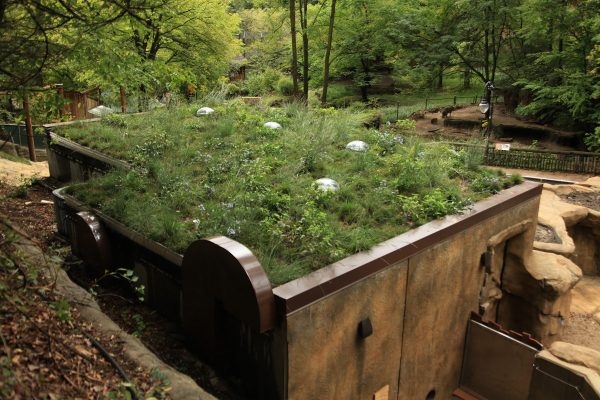
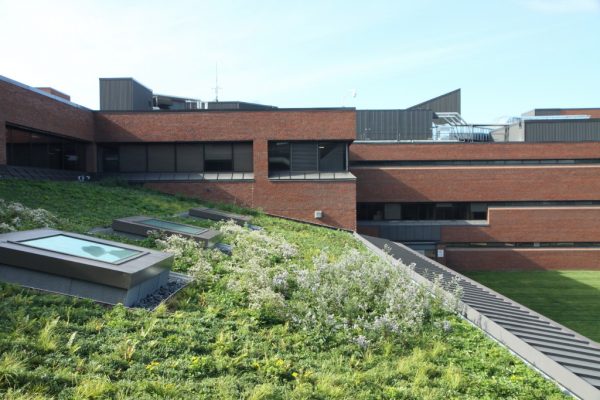
While it is popular to say that native plants are better adapted because they evolved here, this notion is not necessarily true. A plant’s toughness or suitability is dependent upon genetics and ecological and environmental adaptation (evolving with time and exposure). There is nothing magical about latitude and longitude as there may be similar or more demanding environmental conditions on the other side of the globe. In reality, some native plants are tough, some aren’t, and a few will grow in an extensive green roof without frequent irrigation. The list, however, is quite short as the native ecosystem parallel would be a giant rock covered in 2 to 4 inches of gravelly soil with loads of reflected light from bordering rocks. Such real world parallels are few and far between.
Even though the list of native plants for use in extensive green roofs is relatively short, there are a few selections that may grow well as native accent plants with occasional irrigation. In temperate regions of North America, we have recommended natives such as Sedum ternatum (white flowered sedum, a shade lover), Opuntia humifusa (prickly pear cactus), and Allium cernuum (nodding onion).
With regular and frequent irrigation, many others native living roof plants can be sustained. Selections that fall into this category include Echinacea pallida (purple coneflower) and Schizachyrium scoparium (little bluestem). These plants are very drought resistant in conventional landscape settings, because they are great “water sourcers”. On a rooftop with 4 inches of soil, however, they won’t survive for long unless regularly irrigated. Such plants are better suited to the LiveRoof Deep and Maxx systems.
The Bottom Line: LiveRoof growers are interested in using plants that will be successful, regardless of regional nativeness. Rest assured, LiveRoof growers only use plants native to this planet.
How to Specify Green Roof Plants
Start your green roof plant design by contacting your LiveRoof representative for support. The plant palette varies widely across North America with our diverse climates. Even individual rooftops have varying microclimates affected by building height, shading of other structures, wind exposure, reflected light and more.
In cold winter climates, we recommend the following best practices for specifying green roof plant mixes:
In each mix, includes complementary plants, typically 5-9 “Base plants,” and some assortments with “Accent plants.”
Base plants consist of easily propagated deciduous, semi-evergreen, or evergreen Sedums that typically range from ¼ inch to 4 inches tall. They are used to create a beautiful attractive living mulch that serves as a backdrop to any accent plants used in the assortment.
Because base plants are easy to propagate, they may be combined in random mixtures to create a meadow-like effect without increasing the base cost of the LiveRoof system. If the base plants are planted in specific patterns sometimes from plugs), the cost of planting goes up and is reflected in the system price.
Deciduous and Semi-evergreen Base Plants
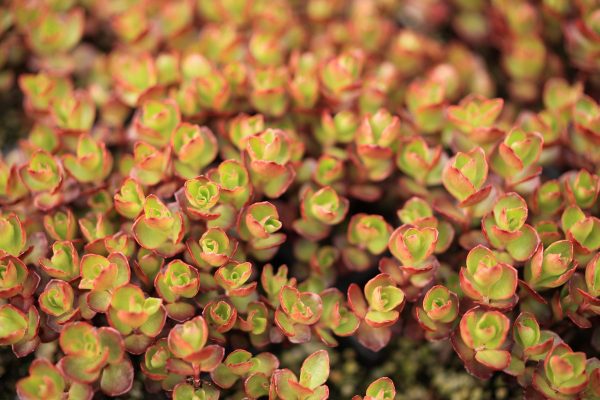
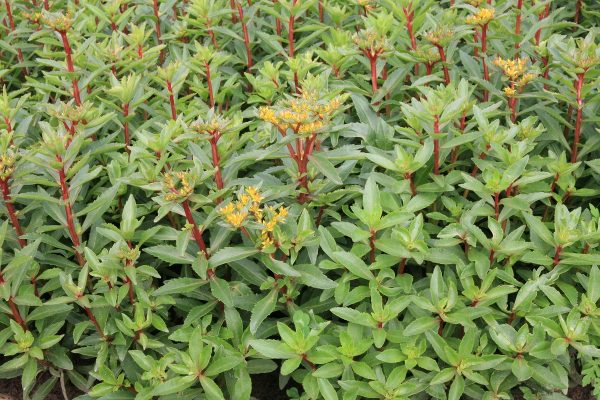
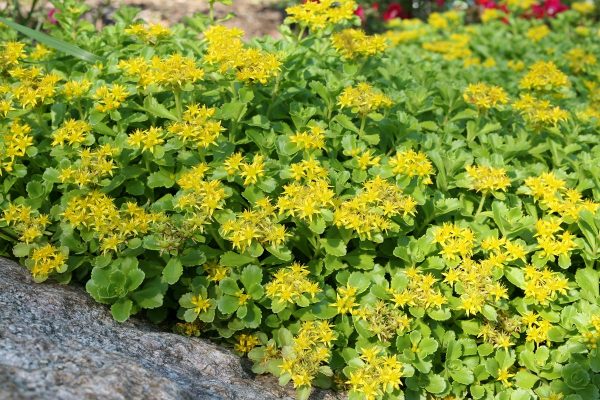
Evergreen Base Plants
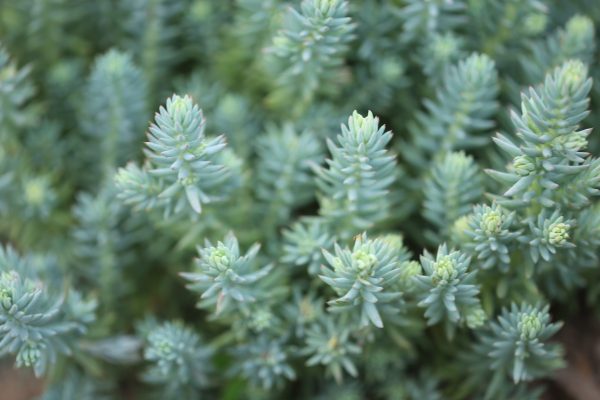
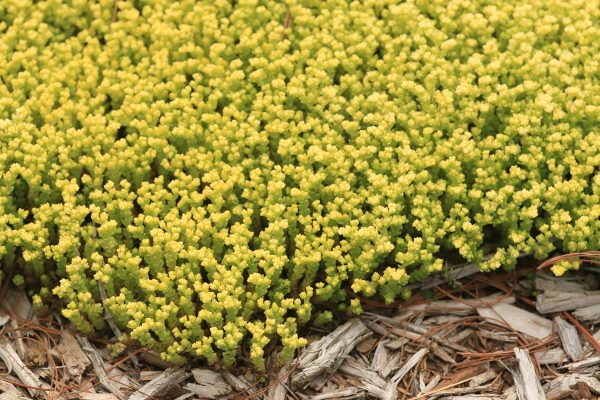
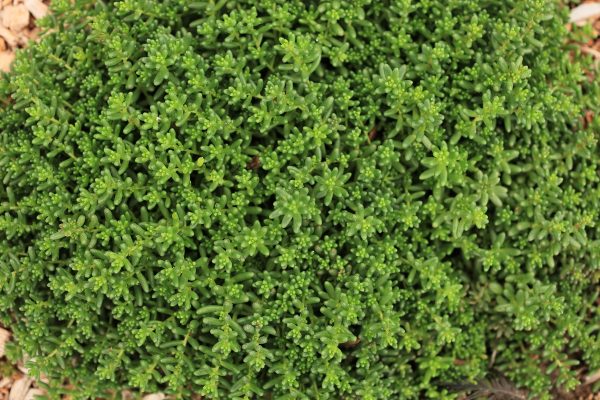
Accent Plants
In addition to a wide selection of base plants, LiveRoof offers an exciting array of accent plants. These accent plants are frequently added to the mix of base plants to create interesting color splashes, vertical dimension, and a unique visual signature.
LiveRoof recommends that accents be planted at densities of ½ to 2 plants per square foot. Depending on density, accent plants typically add from $0.70 to $2.80 per square foot to the overall system cost.
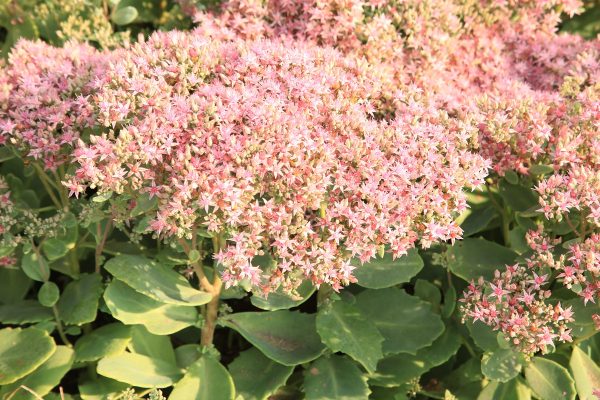
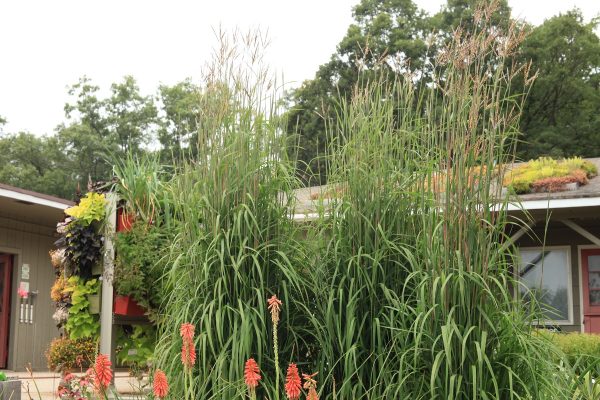
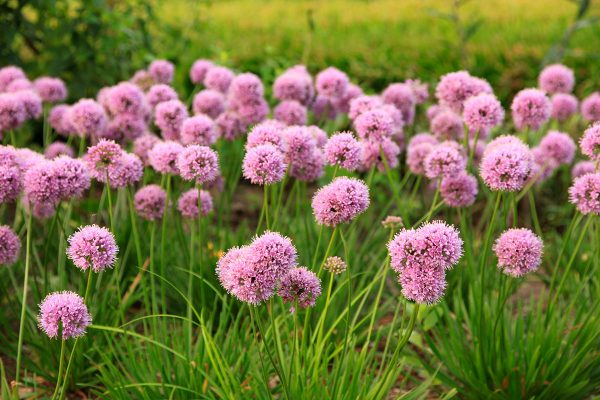
Accent plants from LiveRoof are intended to do the following:
- Create highlights and a unique “Visual Signature” or design impression.
- Draw the eye to particular elements of the LiveRoof.
- Create special effects, logos, or enhance the seasonal aspects of viewership (e.g., flowers during the school year).
Green Roof Plant Evolution Over Time
All plants are unique, and are opportunistic in one way or another. LiveRoof plants are no exception, and practically speaking, some species tolerate heat better than others, some cold better than others, some dry conditions, and others moist conditions. By combining species of varying growth characteristics, we strive to design each LiveRoof plant assortment to perform optimally in all seasons.
Over time, depending upon the particular plant assortment, geographic site, climate and microclimate, the plant assortment will adapt and evolve. One species will increase its presence while another decreases its presence, from season to season, and from year to year. It is this evolutionary dance that helps to make each LiveRoof fresh and exciting now and in the future.
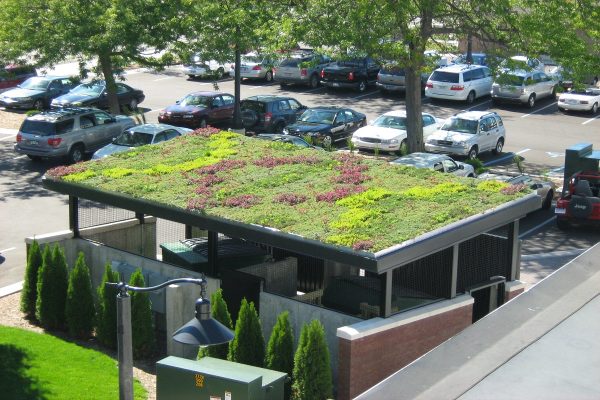
Summer
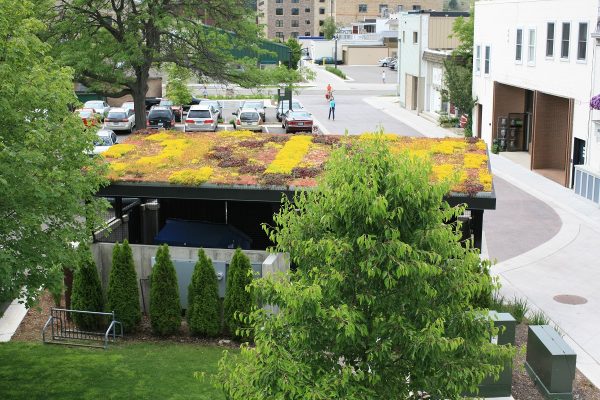
Fall
ROOF MEMBRANES
Retrofit Roofs
Retrofit Projects are exciting as they represent a tremendous upgrade to aesthetics and environmental quality. Of course, they bring their own particular challenges that need to be addressed from an architectural and engineering standpoint. Here are some of the main considerations for retrofit green roofs.
- Determination of the construction, condition, and load capacity of the pre-existing roof and suitability to accept a LiveRoof.
- Determination of the condition of, remaining warranty lifetime, and terms or warranty of the existing waterproofing system as it pertains to being retrofitted with the new LiveRoof.
- Compatibility of the existing waterproofing system with the proposed slip sheet membrane.
- All the same issues regarding positive and negative wind pressure, slope, and forces against the parapet as they relate to new construction also apply to retrofit roofs.
Roof Warranties
LiveRoof is compatible with nearly any roofing system on the market. Over the years, we have seen our system successfully installed atop membranes manufactured by nearly every supplier in North America.
In recent years, more of these manufacturers have decided to introduce their own green roof systems. The quality and the integrity of these systems is variable, thus certain manufacturers have used warranty provisions to limit options for their customers to only system which they sell or market. The most common warranty used to control the green roof options are overburden removal warranties.
Overburden removal warranties cover the costs of removing and replacing the green roof system in the event of a roof leak. To make sourcing a single source warranty easy, LiveRoof, LLC has developed relationships with the following manufacturers who offer single source overburden removal and leak repair warranties:
- Barrett Company (US Only)
- CertainTeed (US Only)
- Flex Membranes (US, Canada)
- Johns Manville
- Sika Sarnafil* (US, Canada)
- GAF (US, Canada)
Other membrane manufacturers may consider adding overburden removal coverage on a case by case basis.
When overburden removal coverage is not available from the membrane manufacturer, LiveRoof Overburden Removal Warranties may be purchased for terms of 10, 15 or 20 years. This warranty provides coverage for the costs to remove the green roof and to replace it after the leak has been serviced. Only Diamond Level LiveRoof Certified Installers are authorized to provide LiveRoof overburden removal coverage. Contact your local LiveRoof representative for referrals to qualified contractors in your region.
* Sika Sarnafil full system warranties may only be installed by Elite LiveRoof Installers and maintained by Elite LiveRoof Maintenance Contractors.
Slipsheet Specifications
The slip sheet is the protective layer used between the modules and the membrane. The material is typically selected and provided by the membrane manufacturer.
For Conventional Membrane Roof Assemblies, we recommend a minimum 1 mm (40 mil) thickness with overlapped and effectively bonded seams to ward against root penetration and to keep waterproofing layer safe from abrasion during installation.
Slip sheet/root barrier typified as follows: Welded Seam Types – 1 mm (40 mil) or greater thickness
-TPO, with seams heat welded
-PVC, with seams heat welded
-Polypropylene, with seams heat welded
-HDPE, with seams heat welded
Glued Seam Types – 1 mm (40 mil) or greater thickness
-EPDM, with seams overlapped a minimum of 75 mm and glued with roll out adhesive or double sided tape adhesive of the type that is impervious to and not affected by moisture, and recommended by the manufacturer.
-Low profile drain board of appx. 0.5 mm (17 mil) thickness, with edges overlapped 75 mm and glued with manufacturer approved adhesive.
For Protected Membrane Roof Assemblies, we recommend a minimum .25mm (10 mil) thick slip sheet of woven polyethylene or other non-moisture holding material to be installed above the membrane and below the insulation, as specified by membrane manufacturer.
A minimum .25mm (10 mil) thick slip sheet of woven polypropylene or other non-moisture holding material to be installed above the insulation and below the green roof modules, as specified by membrane manufacturer.
Do not use duct tape or adhesive for seaming that is not approved by the membrane manufacturer. Never use moisture holding fabric, such as needle-punched polyethylene or felt, under the green roof system. Such materials are trap aggregate and are impossible to sweep during installation and stay wet and encourage root growth and root penetration, which is especially detrimental if woody plants become established as such plants have woody root systems and may potentially cause roof leaks. This could lead to impeded drainage and compromise plant health.
In cases where electronic leak detection may be desired, a fiber-backed drainboard may be used. Fiber-backed drainboards are only recommended when electronic leak detection is desired, and only when vegetated with Sedums or Sempervivums, or other succulents, as these plants are sparsely-rooted and not prone to rooting into the fiber of the drainboard.
Need help selecting compatible roofing assemblies? Your local LiveRoof representative can help.
STORMWATER MANAGEMENT
From the perspective of civil engineers and city planners, the capture of rainfall may be the greatest perceived benefit to green roofs. Sewage infrastructure and retention tunnels are expensive, and green roofs can have a significant impact on reducing the need for such infrastructure.
Runoff Basics
It is common to ask how much water the LiveRoof system will absorb. Or, how much of the initial rainfall (e.g. first ½ inch, ¾ inch, etc.) will be absorbed prior to system saturation and run off. The answer must always begin with five words:
“It depends upon many variables.”
Annual Rainwater Absorption
Most research (Liesecke, 1998; Moran et al., 2004; DeNardo et al., 2005; VanWoert et all, 2005) has shown an annual runoff reduction of 60-100%, impacted most significantly by climate. The precise amount for any given locale and any given rooftop is not one size fits all. The factors that come into play are numerous and include the following:
- Regional Precipitation
- Seasonal Weather and Rainfall Patterns
- Rainfall Intensity
- Wind and Sun
- Roof Slope
- Soil Depth
- Soil and Plant Characteristics
- Typical Growing Medium Characteristics
- Supplemental Irrigation
Regional Precipitation
Use the images below to estimate your region’s precipitation. For a more in depth review of precipitation for your region, click the image to visit the National Weather Service website.
Source: AHPS Precipitation Analysis, National Weather Service (weather.gov)
Source: Accumulated Precipitation, Agriculture and Agri-Food Canada (agr.gc.ca)
Seasonal Weather and Rainfall Patterns
When comparing the average monthly rainfall and daily average temperatures of various cities, the differences are amazing. In Phoenix, temperatures tend to be hot and what little rain falls is spread evenly over the year. In Portland Oregon, the temperatures tend to be moderate with wet winters and dry summers. In Chicago and New York the winters are cold, spring and fall are cool, and the summers are hot; precipitation is spread pretty evenly throughout the year. Miami is warm in winter, hot spring through fall, and has a defined summer rainy season where rain can fall in torrents. With this in mind, each climate will have different absorptive qualities. A city like Phoenix may experience nearly 100% rainfall retention, because it is typically hot and dry with little rainfall. Cities like Chicago or New York may see annual stormwater retention in the range of 60% to 85%. And a city where the rain comes in torrents will experience less annual rainfall retention. Retention will also vary somewhat from year to year as determined by the year’s weather.
Rainfall Intensity
Soil acts as a sponge in capturing and holding onto water. But, soil is less porous than a sponge, and will take longer to absorb and hold onto water. For this reason, if a rain event is very fast and intense, such as 1 inch over 15 minutes, a certain amount of water may sheet across the soil surface to the roof drains, before becoming absorbed by the soil. On the other hand, if a 1 inch rain comes in a gentle soaking drizzle over the course of a couple of hours, the efficiency of water capture is much greater.
Wind and Sun
Windy sites, particularly those that are windy during hot dry weather, will dry out more and retain more rainfall on an annual basis. Taller buildings will tend to be windier and those with reflected light or heat will dry out faster and therefore absorb more water as well. Of course, all things being equal, sunny areas are going to have less stormwater runoff then shady areas.
Roof Slope
All roofs must slope in order to drain, and what most people refer to as a flat roof will have a slope of ¼” per 12’. Such roofs will retain more water than roofs with greater slope. This is because soil holds water by cohesion, but there is a limit to how much cohesive force soil can provide.
Practically speaking, soil acts as a sponge. If a moist sponge is angled upward, additional water will run out of it. The same is true of soil. The greater the angle, the less capable the soil is of retaining water.
Researchers Bradley Rowe, Kristin Getter, and Jeffrey Anderson have conducted studies regarding slope and water retention with inclines of 2%, 7%, 15%, and 25%, and found that annual water retention in Lansing Michigan ranged from approximately 85% with 2% slope to 76% with 25% slope.
Soil Depth
One might logically presume that the deeper the soil substrate the more storm water a green roof will mitigate.
This is not necessarily true as independently discovered by Dr. Bill Retzlaff, et. al., of Penn State and Civil Engineer Drew Gangnes of Magnusson Klemencic Associates of Seattle have published their findings that a 4 inch soil depth performed optimally for storm water retention.
An extensive green roof with a 4 inch soil depth has the combined ability to hold water along with the ability to evaporate water between rain events, resulting in the least amount of runoff. In comparison, a 6 inch system might hold somewhat more water, but won’t dry out as effectively between rain events and a 2-½ inch deep system may dry faster but won’t hold as much rainwater.
Soil and Plant Characteristics
Plants and Soil also play a role in stormwater retention. Soil aggregate sizes and composition affect pore space, air space, and absorptive capacity. The volume and type of soil will also influence each system’s ability to absorb water.
And, while soil is mostly inanimate, it will gradually change over time due to natural freeze-thaw cycles that can alter particle sizes of some of the mineral components.
Neither is the organic component static and can either rise or fall and therefore affect the soil’s absorptive capacity. The process of plant growth and decay (leaves roots and stems) can contribute organic matter, particularly deciduous plants which shed their leaves to nourish the soil. Fully evergreen plants on the other hand may actually reduce organic matter from the soil. Plants also affect water retention and runoff by their use of water. They extract water from the soil and combine it with CO2 to make sugars, and they liberate water to the atmosphere by transpiration (similar to sweating) when it is sunny and there is sufficient water available.
In either case, plants help to keep rainwater out of the stormwater system and the more densely they cover the soil surface, the more absorptive capacity they have.
Typical Media Characteristics
Density Measurements
Analysis | Units | Results |
---|---|---|
Bulk Density(dry weight basis) | g/cm3 | 0.97 |
lbs/ft3 | 60.37 | |
Bulk Density (at max water-holding capacity) | g/cm3 | 1.44 |
lbs/ft3 | 90.21 |
Water/Air Measurements
Analysis | Mass | Results |
---|---|---|
Moisture (as received basis) | % | 21.0 |
Total Pore Volume | Vol % | 58.8 |
Maximum Water-Holding Capacity | Vol % | 48.3 |
Air-Filled Porosity (at max water-holding capacity | Vol % | 10.5 |
Water Permeability (saturated hydraulic conductivity) | cm/s | 0.018 |
in/min | 0.434 |
Effect of Supplemental Irrigation
While irrigation is used to sustain the LiveRoof system during hot dry periods, a particular roof will likely experience little reduction to its absorption of stormwater. Typically irrigation is used, temporarily, during times of sparse rainfall and the added water is mostly evaporated or sequestered by the plants.
Green Roof Rainfall Retention Research
The map below contains data and information links for rainfall absorption rates from studies performed across North America.
Stormwater Project Size Calculator
If you are aware of how much stormwater storage you need in your next project – we can help you calculate the approximate project size needed to achieve those goals. Including with and without our RoofBlue RETAIN accessory.
Contact a sales representative in your area to discuss your stormwater storage needs and we will help you calculate the size of your project. We also have expertise in plant selection, helping you to choose plants for the system that best accomplishes your objectives.
SLOPED ROOFS
The combination of a green roof (unaffixed object), slope, and gravity imply the need to address physical containment and resistance to downward pressures exerted by the green roof against the parapet and mechanical fixtures of the roof especially in cold climate areas where ice crystals may form on the slip sheet/root barrier surface during winter. For this reason, LiveRoof recommends that the slope and size of the roof be assessed in regard to force that will be exerted against the parapet or other mechanical features of the roof.
For the convenience of engineers, LiveRoof provides force tables for use in designing each particular LiveRoof project.
Downward Force Against Parapet For Sloping Applications
These tables assume “zero” friction and present a conservative model based upon the assumption of ice between the slip sheet membrane and the LiveRoof modules during the winter months. Obviously, this may not be appropriate for frost free zones, but one must realize that certain roofing membranes are coated in talc or other lubricants to prevent sticking. Others membranes may be slippery when wet. Therefore, even in frost free zones, one should assume a degree of downward force on sloping applications.
For long roofs and roofs with great slope, it may be appropriate to incorporate “stops” or buttresses in the design to prevent all of the load from being exerted against the parapet on the low side of the roof. In all cases, it is important to realize that the low side parapet must be built in such manner as to have the structural integrity to resist whatever forces exist given the design of the particular roof.
How Much Slope is too much?
Both of the main international green roof organizations, the German FLL and North America’s Green Roofs for Healthy Cities agree that green roofs should not be applied to roofs with slope of greater than 40 degrees. This stems both from containment challenges but also from the extreme difficulty in managing soil moisture on a roof of such pitch.
You may be familiar with the properties of a wet sponge, where it will hold so much water when laying on its side. But, after you prop it up on its end even more water runs out. Soil acts the same way and as the pitch of the roof increases, there is a greater tendency for the water to want to run out of the system. Green roofs above 2’/12’ pitch are commonly dry at the top and moist at the bottom. And, while the segmental or baffled characteristic of LiveRoof may help to mitigate this phenomenon, pitched roofs will certainly require more irrigation than low sloped green roofs.
How Much Slope is too little?
While this question is seldom asked, it is important to design for adequate drainage. Most authorities state that a roof needs ¼”/12’ slope to provide adequate drainage. Without this, water may accumulate and damage the health of your LiveRoof plants.
Level or Gently-Rolling?
Most LiveRoof installations simply follow the contour of the roof for a lovely, gently-rolling, meadowlike appearance. If a dead-level LiveRoof is required, it can be realized by applying a tapered closed cell foam to the roof above the waterproofing layer. If this is done, the closed cell foam must allow for adequate water drainage.
Using LiveRoof and foam as a lighter alternate to soil-filled planters
LiveRoof can be used as a lightweight alternative to deep planters filled with soil. Many designers want to break up space and/or add seating with taller planters, while reducing the overall load on the roof. Layers of insulation can be cut to fit to fill the planters, and the green roof modules placed atop it.
EPS foam is typically specified for this purpose. We recommend selection of the most economical appropriate underlying product which will hold up long term, and we highly encourage specifiers to investigate comparative costs prior to specifying the type of underlying foam used in these planters. The selected materials should be suitable for occasional foot traffic and the weight of the vegetative module as well as a snow load, if applicable in the climate:
LiveRoof Lite Module Saturated Weight: Appx. 15-17 lbs/sf saturated and vegetated
LiveRoof Standard Module Saturated Weight: Appx. 27-29 lbs/sf saturated and vegetated.
LiveRoof Deep Module Saturated Weight: Appx. 40-50 lbs/sf saturated and vegetated
LiveRoof Maxx Module Saturated Weight: Appx. 60-65 lbs/sf saturated and vegetated, when filled with LiveRoof Engineered Soil
Working on a sloped green roof? Your local LiveRoof representative can help.
Example Sloped Roofs
WIND RESISTANCE
Wind Pressure
As with any roof, high winds can pose a threat to the security of green roofs, and care must be taken to properly design and engineer the green roof so that it retains its integrity during high winds. To do this, consideration of wind pressure and associated variables, such as the building’s geographic location, surrounding terrain, shape, slope, height, building openings, parapet design, and other features is essential.
At the tip of the iceberg, of wind pressure, one must consider the typical high wind speeds for that region. Consulting ASCE 7.95 Figure 6-1 Basic Wind Speed, or Factory Mutual Global Property Loss Prevention Data Sheet 1-28 is a good first step. In addition, the engineer must consider the surrounding terrain; for example, is the building situated along water, mountains, open field, surrounded by tall trees or taller buildings?
Of course the building design itself is very important. The National Fire Protection Association defines “high-rise building” as a building greater than 75 feet (25 m) in height where the building height is measured from the lowest level of fire department vehicle access to the floor of the highest occupiable story. Low rise buildings (75 feet and lower) are less affected than high rise buildings (greater than 75 feet) which in addition to direct (positive) wind pressure are more greatly affected by negative wind pressure, often referred to as uplift or suction.
LiveRoof offers WindDisc™ as a simple way to connect LiveRoof modules and/or RoofStone pavers.
Positive Wind Pressure
Positive Wind Pressure is the force exerted by the wind as it strikes an object, or building. Positive Wind Pressure is evident when a tree (or other object) moves or bends over in a strong wind.
LiveRoof modules, when populated with a base mixture of flexible-stemmed hardy sedums (the backbone of the LiveRoof product line) were wind tested on 1/25/08 with wind speeds exceeding 110 MPH. In this test, the LiveRoof planting (4’ x 5’) was surrounded with RoofEdge edging and first exposed to 10 minutes of wind at 95 MPH, followed by 1 hour and 50 minutes at 110+ MPH. The wind was impinged directly upon the surface of the LiveRoof planting as would be the case when testing other roof coverings. Remarkably, at the end of the test period, there was no loss of growing medium and all plants remained well rooted and intact. Throughout the test, the plants simply arched over, held in place by their root systems. This test demonstrated the value of full vegetative cover as a means of stabilizing the green roof system.
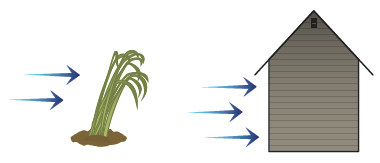
Negative Wind Pressure/Uplift
Negative Wind Pressure is what causes airplanes to fly, and it’s what causes roofs to want to fly. Negative wind pressure occurs when wind passes over an object that causes the wind to redirect and accelerate. This in turn creates a pressure differential and the pressure differential can be substantial.
In the case of roofs, wind accelerates as it passes over the roof edge or parapet, causing a pressure differential and lifting force, uplift, that is exerted upon the rooftop. Redirected winds of this nature tend to whirl and swirl, often in cone shaped vortices which can aggressively scour roof surfaces and components. Such forces are typically greatest in the corners of the roof, secondarily along the parapet walls, and to a lesser degree in the “field” or center part of the roof. Uplift forces vary with the building shape and height, parapet shape and height, overall exposure, size of openings, etc.
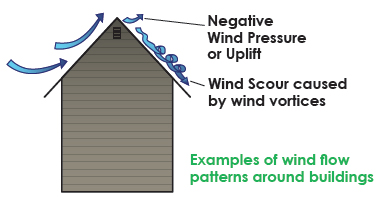
Wind Resistance Testing Standard
The Canadian Standards Association (CSA) launched CAN/CSA A123.24-15 in 2015 as a testing standard to determine response of a vegetated roof assembly (VRA) to Wind Pressure and Wind Flow. The standard defines a VRA as the modular vegetated system (pre-grown vegetation in the form of modules, blankets or mats, growth media, root barrier, pavers and drainage system) and the roofing system (deck, membrane, vapor barriers, insulation coverboard, etc.). Membranes must be fully adhered.
This standard may only be used to test modular or thin-layer mat systems where all the soil is contained in the mat and which are installed with at least 80% vegetation coverage. This means that built-in-place systems planted with plugs, tiles or mats may not be tested under the current standard.
Wind Pressure Test
To test for Wind Pressure, a full scale uplift chamber evaluates the ability of a vegetated roof assembly to resist a series of simulated “wind gusts” where pressure builds and subsequently drops. This test method is used to determine the amount of fatigue and uplift response of the green roof. The National Research Canada (NRC) conducted wind pressure tests on two LiveRoof assemblies in December 2015. Both assemblies sustained wind uplift pressures of 200 psf. The rating is issued after a 1.5 experimental factor, so the systems tested have an uplift resistance rating of 133 psf (6.36 kPa) under this standard.
Wind Flow Test
To test for Wind Flow, a high powered wind turbine evaluates the ability of a modular vegetated system to resist sustained high speed winds. This test method is used to determine the level of sliding, overturning or scouring of the green roof. During an October 2015 testing of LiveRoof system, the assembly sustained winds until the turbine maxed out during the 210 km/h cycle. The rating is issued based upon a 1.5 experimental factor, thus the system tested has a flow resistance rating of 83 mph (133 km/h) under this standard.
Wind Design Standards
In 2010 the American National Standards Institute (ANSI) accepted RP14 Wind Design Standard for Vegetative Roofing Systems as an American National Standard. This document provides design and installation recommendations to mitigate the risk of wind uplift on green roofs in high wind areas. LiveRoof modules are fully vegetated at the time of installation and have subterranean overlapping lips, which allows them to be sheltered from direct wind exposure. The LiveRoof Lite System is 2.5” deep and has a dry weight of approximately 10 lbs per sq ft, and thus meets the definition of #4 Ballast (3.13.1). The deeper Standard (4.25”), Deep (6.25”), Maxx 8” and systems meet the definition of both#4 Ballast and #2 Ballast (3.13.2).
Parapet Design
Low rise buildings in areas of moderate exposure may present fewer challenges in regard to Positive or Negative wind forces. But, taller buildings may cause one to have to be more creative. Design strategies that moderate wind uplift forces and disrupt the formation of surface-scouring wind vortices may be employed in the overall green roof design.
Regarding low rise buildings, a lower parapet design may avoid potential air turbulence and help to minimize uplift forces. And, for buildings containing only a single parapet, as is commonly used as a facade for aesthetic purpose, one should keep in mind that the parapet may dramatically increase the uplift pressures in the corner regions. Conversely, on high rise buildings (over 60 feet), higher parapet height can be an effective tool in moderating uplift forces. Studies on parapet height typically indicate that parapets over 3 feet tall can moderate uplift pressure in the corners of the roof on high rise buildings. Likewise, the use of a partial parapet with attached porous screen may be used to reduce uplift pressures and expand design options for taller buildings. And, parapets of different shapes, e.g. saw-tooth configuration, rounded vs. sharp edges, or the application of spoilers are sometimes used.
Keep in mind, that the taller the parapet, the more Positive Wind Pressure against the parapet itself, both windward and leeward sides.
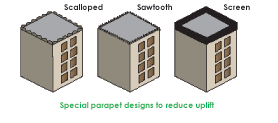
Wind Challenged Applications
In very challenging applications an engineer may have to direct the architect to forego using the LiveRoof Lite system (about 9 to 10 lbs per sf when bone dry) in favor of the LiveRoof standard system (about 18 to 20 lbs per sf when bone dry). And, in the most wind challenged applications, an added means of securing the LiveRoof (either LiveRoof Lite or Standard) may be needed to safeguard the LiveRoof system. Accessory products for extreme uplift designs may include any or all of the following.
- Using the lab-tested WindDisc™ solution in all or the most uplift-prone zones of the green roof.
- Limiting the LiveRoof to the center “field” of the roof top, and using heavier ballast in the corners and along the parapet edges. Such ballasted perimeter design is referred to as a “vegetation free” zone. Vegetation free zones will vary with the parapet height and geometry.
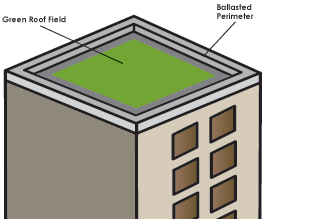
Tall Buildings: How High is Too High?
Tall buildings present three substantial challenges for green roofs. The first is wind uplift. This is a physical phenomenon that presents certain design and engineering considerations, discussed in detail under the wind uplift section.
The second is wind scour. This is the physical displacement of soil and/or plants due to the force of the wind. The best defense against wind scour is full vegetation, which LiveRoof provides. It is also important to remediate any “bare patches” that might arise in the future. Bare patches can be caused by weed encroachment, nesting, birds, or physical damage.
The third challenge involves the plants and their ability to resist the wind and cold at high building elevations.
The answer to the question “how high up can green roof plant survive?” is not well understood, at least not at this time. Very tall buildings, for example over 20 stories tall, are subject to virtually constant wind. This in itself is not a problem as it can easily be offset with irrigation, and we would consider a built-in irrigation system mandatory on any tall building regardless of climate.
At the present time, the level of experience and bona fide research with green roofs on tall buildings is limited. No one can say “on the 35th floor in New York City, you can effectively grow these five species of plants.” Therefore, at present we must rely upon anecdotal experiences, common sense, and horticultural know-how.
The tallest LiveRoof brand green roof, to date is on a building that is 630 feet (58 stories) tall in Chicago, Illinois. Installed in 2014, it used the WindDisc system to connect the modules together across the installation. The plants were selected for their performance on other tall roof applications, and this “High Rise Mix” has performed well in this extreme environment.
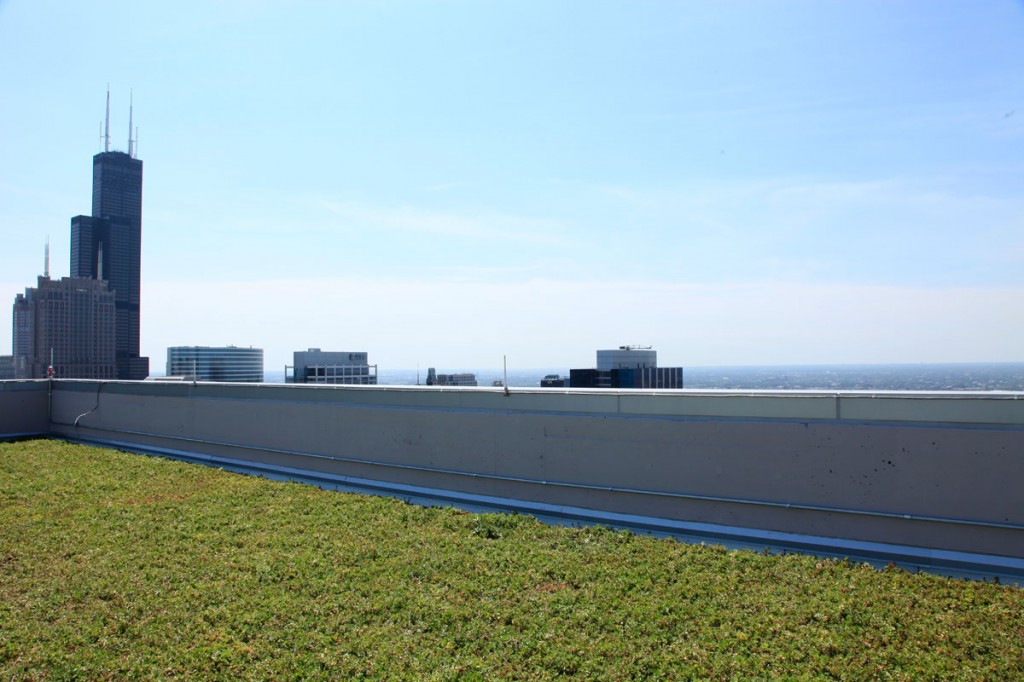
We suggest the following:
Going forward, we suggest that green roofs be applied to tall buildings with a cautious and thoughtful approach. Use the toughest, most cold-tolerant species, install them early in the season to allow for acclimatization to winter, and always incorporate a built-in irrigation system into the design. Work with the local LiveRoof representative to determine whether WindDisc™ or other uplift mitigation measures are required and to ensure that proper plants are selected for your high-rise application.
Wind-VRA
National Research Canada has published a Wind-Roof Calculator on Internet for vegetated roofs to calculate roof cladding wind loads and vegetated roof assembly design parameters based on the National Building Code of Canada 2015.
Not sure if you need WindDisc®? Your local LiveRoof representative can provide more details on the results of tested and expected wind resistance of our various green roof systems.
ADDITIONAL DESIGN RESOURCES
LiveRoof® BIM Components for the LiveRoof Standard, Lite, Deep and Maxx Systems are available on our details page.
Continuing Education
LiveRoof Global is pleased to provide an AIA-approved continuing education course. Course participants will experience content including types of green roofs, benefits and elements of green roof design as well as things to avoid when designing and installing green roofs. Examples of green roof projects are used to illustrate concepts as they are introduced.
Visit our Continuing Education page for more information.
We mention the above considerations as an impetus to diligent design and engineering, but do not purport to have specific knowledge of engineering principles. Such expertise and accompanying liability is the domain of qualified engineers. We will continue to pioneer new research to continue to provide improved support services to engineering professionals. For now we offer these considerations to stimulate a diligent review of design and engineering considerations as they pertain to green roofs.
Couldn’t find the answer to your question? Contact us!